The foundry's secret
Release time:2023-11-17
The foundry's secret
Casting is an ancient metalworking process dating back 6,000 years. Industrialization and the advancement of product technology have promoted the development of the foundry industry. The sound development of the casting industry has put forward higher standards for various mechanical and physical properties and mechanical processing properties of castings. For pig iron castings, how does the foundry deal with it?
(1) Pouring
In the casting process of pig iron, the phenomenon of choking is often caused by pouring too fast. Therefore, the foundry will choose the "long stream" method at the beginning of pouring, slowly pouring, and then speed up the pouring flow until the pouring model is filled with metal liquid, but still to prevent the occurrence of metal liquid spillover. In the later stage of pouring, continue to choose the slow pouring method, until the metal liquid reaches the top of the model, slowly collect the bag.
(2) Making castings
In the casting process, the foundry usually covers the template with a layer of plastic film, and the gas inside is extracted through a vacuum pump, so that the film can be tightly attached to the template. Then put the template on the sandbox, and fill the molding data into the sandbox. Through vibration and scraping, the plastic film covers the top surface of the sand box, and then extract the air between the sand particles, so that the negative pressure is formed in the sand mold, and then remove the template vacuum, so that the plastic film can be adsorbed on the surface of the inner cavity of the mold, and the sand mold has a certain strength and hardness by the effect of pressure difference. Then, after mold drawing, box closing, pouring, condensation cooling and withdrawal of negative pressure, the required castings can be obtained.
(3) Casting defects
In the process of producing cast pig iron in blast furnace, there are some common casting defects, such as hollow iron, slag iron, vortex iron and so on. The causes of different casting defects are different.
1. Hollow iron
Cause: Hollow iron is caused by the gas precipitated in the shrinkage hole and pig iron ingot when the iron liquid is solidified, and the air involved cannot be fully discharged.
Improvement measures: you can choose to slow down the pouring flow rate during pouring, reduce the involvement of air, control the solidification state of pig iron ingots and other measures to solve the problem.
2. Slag iron
Cause: The slag in the slag iron mainly comes from the slag that can not be separated in the iron liquid and the slag involved in the flow channel;
Improvement measures: Measures can be taken to stabilize the temperature of the iron liquid out, ensure the smooth flow of the iron liquid, and enhance the separation and storage of iron slag to solve the problem.
3. Vortex iron
Cause: The whirlpool iron is mainly formed by the moisture attached to the mold cavity is not dry, and it boils sharply after meeting the iron liquid, making the iron liquid roll in the mold, and is formed with the gradual cooling and solidification of the iron liquid;
Improvement measures: The method of strictly controlling the spray process and ensuring the preheating temperature of the iron mold is used to solve the problem.
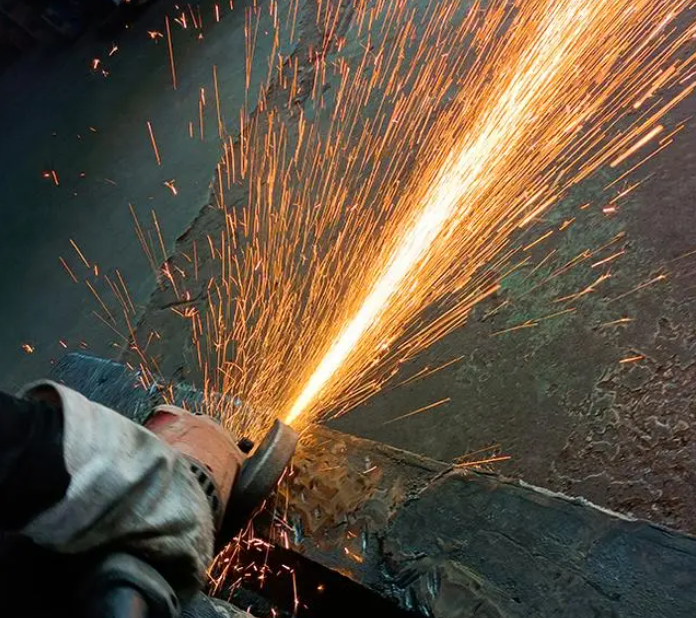