What's the difference between die casting and extrusion?
Release time:2023-09-18
What's the difference between die casting and extrusion?
What is the difference between the principle of aluminum extrusion and aluminum die casting? Today, we compare the production equipment and production process of aluminum die casting and aluminum extrusion and the cost of these two materials to take a look at aluminum die casting and aluminum .
What are the differences?
There are three main ways of making aluminum:
1, aluminum casting
2, aluminum extrusion
3, aluminum die casting
Casting: Should be said to be the most inappropriate way
Casting is to melt the metal material after casting into the casting mold molding, but there are many problems that may occur between solid and liquid molding, mainly in the molding is likely to leave bubbles, the strength is very
Bad (in fact, it doesn't work at all) is a difficult and expensive way of manufacturing. But the biggest advantage of casting itself is that it can be made into a variety of complex shapes.
Aluminum extrusion: The most cost-effective, difficult and low production method
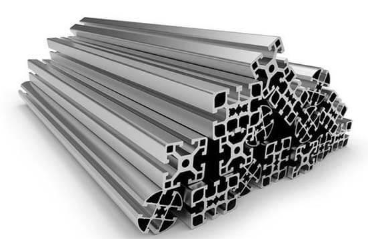
Aluminum extrusion is to extrude aluminum ingots (processed alloy raw materials) at a plastic temperature of about 5 to 600 degrees, low technical threshold, low cost, production speed is very fast, and the strength is related to the material characteristics of aluminum alloy. But there should be some degree of intensity. However, the disadvantage of extrusion is that the shape is simple, and only cross-cutting sections can be made to fix the same thing, so complex shapes and variable surfaces can not be extruded
Aluminum die casting: should be said to be the most ideal production method
The strength of the die casting can be strengthened, for example, many parts on the bicycle are made by die casting. However, there are many ways to die casting, in the production must consider the production efficiency, production difficulty, production cost, etc. Whether there is a process to adapt to die casting, whether it is necessary to die casting process, whether it is necessary to die casting production, whether it is in line with the cost.
General die casting is by oil pressure injection, according to the total force of the mold injection, pressurization total for its maximum ton, such as 800 tons is the most common, 1200 tons up even another grade, the general maximum is 3000 tons.

1, cold chamber die casting and hot chamber die casting
The difference is in the mold temperature control, the cold chamber is mostly small and thick parts, and the hot chamber is large and thin parts.
2, general die casting and vacuum die casting
The difference in the vacuum die casting product is dense and can be polished anode and heat treatment, general die casting can not anode and heat treatment, easy to multiple defects.
3, general die casting and soup forging
Molten forging should be the rise of the past ten years, similar to the principle of die casting, mainly in the rate of fire molding is slower, and multi-phase, mostly no stage rate of fire, and the general die-casting fixed two-phase or three-phase pressurization is different, die casting rate of fire is more than 10 meters per second speed, high pressure and high-speed forming. The molten soup is less than ten meters below, the rate of fire varies according to the different mold filling, the molten soup forging part of the finished product and the die casting parts are generally not heat treatment, and the surface will also bubble. There are a lot of special die-casting, extrusion or powder molding, etc., there are also precision casting semi-pressing semi-casting some special production of alternative small parts.