Effect of cooling water on die casting life and casting quality
Release time:2023-10-18
Effect of cooling water on die casting life and casting quality
The influence of cooling circulating water in die casting mould on prolonging die life and improving casting product quality was analyzed, and the requirements for cooling circulating system were put forward.
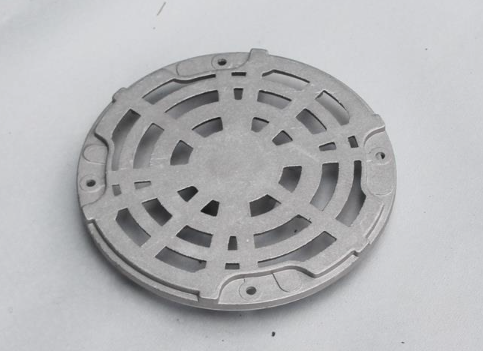
Die casting refers to the use of die casting machine to inject aluminum, zinc, magnesium, tin and other alloy molten liquid into the mold in the molten state of pressure forming and forced cooling, in a short period of time to produce a large number of castings with high dimensional accuracy and good internal structure density, in order to reduce machining allowance and ensure the internal quality of castings. Therefore, the rational use of circulating water for mold cooling is particularly important in complex die casting molds.
2, the influence of circulating cooling water on die casting mold
The cooling of die casting mold can be divided into external cooling and internal cooling. The external cooling is to spray the surface of the mold cavity with the nozzle after the casting is released, and spray the release agent. Internal cooling is circulating cooling water inside the mold, which is the main cooling method of the mold (see Figure 1). In the domestic aluminum cylinder die casting project of Dongfeng Honda Engine Co., LTD., the moving core of the complex cylinder die casting mold and most of the hole making pins have cooling water inside to control the temperature of each part of the mold.
Although the temperature control of the mold is high, it is conducive to the filling of liquid aluminum in the mold and conducive to the forming of the casting, but when the mold temperature is close to 300℃, there will be obvious aluminum sticking phenomenon, so that the surface of the casting is rough or missing, and the mold needs to be polished frequently. At the same time, the casting is not sufficiently cooled in the predetermined time to open the mold, the casting due to insufficient cooling and mold clearance is not fully formed, coupled with the phenomenon of aluminum sticking, the mold will lead to the module and hole pin force is too large and tear damage (the sound of opening the mold will also increase significantly). Too low mold temperature control will affect the fluidity of aluminum liquid and cause cold isolation of casting. We hope that the temperature of each part of the mold should not be too different, otherwise the module cracking will be caused by the uneven thermal expansion and cold contraction of the mold, and the small cracking will continue to expand due to the phenomenon of stress concentration and the infiltration of liquid aluminum, so that the module partial cracking will directly affect the service life of the mold. In production practice, we have encountered scale caused by poor cooling water quality and caused partial cooling tube blockage, resulting in the movable core on the side of the moving mold
The high sub-temperature (surface temperature close to 300℃) leads to serious aluminum sticking on the surface of the mold cavity, and the mold has to be polished almost every shift, and the cracking phenomenon at the corners of the module has increased significantly. Through the measures taken to clear the pipes and improve the water quality, the situation has improved significantly.
3. Influence of mold cooling water on casting quality
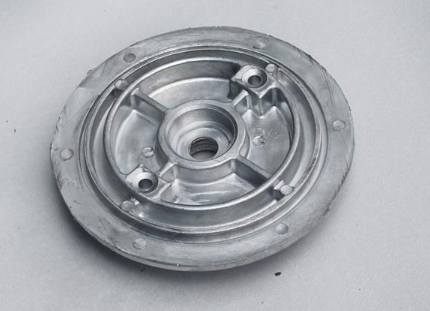
The temperature of each part of the mold varies according to the need, the aluminum liquid in the part with larger wall thickness solidifies slowly, and the mold temperature can be slightly lower; In order to prevent cold isolation at the rib plate, convex part or thin wall, the mold temperature should be relatively increased to improve the flow of aluminum liquid. Controlling the temperature of each part of the mold can also change the distribution of shrinkage holes in the casting (see Figure 2). The aluminum cylinder body blank produced by us is prone to shrinkage between the water jacket and the bolt hole, resulting in leakage between the water channel and the bolt hole. If the cooling of the hole making pin is strengthened, the aluminum liquid around the bolt hole can be accelerated to cure, while the other parts are cooled slowly, and the shrinkage hole is always formed in the position where the aluminum liquid solidified. The shrinkage between the water jacket and the bolt hole is transferred, and the leakage rate of the casting is controlled.
Poor mold cooling makes the mold temperature high, in addition to causing sticky aluminum affecting the surface finish of the workpiece, it will also produce tensile stress during demoulding because the workpiece is not sufficiently cooled and formed, resulting in internal dark cracking. In the production of cylinder block blank die casting, we have encountered obvious leakage phenomenon in the pressure test of blank due to poor cooling of fixed die.
In order to reduce the porosity in the casting, the mold must have a certain volume of riser and a perfect exhaust channel. The exhaust gap between static and static molds is too small, and the air in the mold cavity cannot be fully discharged during the filling process of aluminum liquid, which will increase the porosity in the casting; If the gap is too large, the aluminum liquid will rush out of the gap, forming too large a flash. In order to solve the contradiction of smooth exhaust and no leakage of liquid aluminum, water cooling pipe can be added to the cold iron at the outer exhaust part of the riser. When the aluminum liquid can smoothly discharge the mold cavity gas through the riser from the large gap of the airway, the aluminum liquid can quickly condense in the cold iron with internal cooling without causing too much burr. In order to enhance the cooling effect of the cold iron, in addition to the use of cooling water, some also use high thermal conductivity alloy materials.
4. Cooling water system
In order to ensure the clean water quality of the existing mold cooling water, we use closed cooling tower circulation system; In order to avoid scale clogging the pipeline, the circuit is equipped with a multifunctional high-frequency electronic scale-removing device and a medicated anti-corrosion device. In order to prevent rust, the metal components in the reservoir are all made of stainless steel, and the suction port is a certain distance from the bottom of the pool, so as not to inhale sediment. According to the needs of the cylinder mold, the cooling capacity of the cooling water system is 100RT (RT-Japan cold ton, 1RT=3320kCal/h=3.861kW). The large cooling water circulation is 13090L/min, the water supply pressure is 0.3-0.4MPa, the water supply temperature is 20-35℃, and the temperature difference between import and export water is 5℃.
During the training at Honda Motor Co., Ltd. in Japan, we carefully observed and analyzed the cooling water system of the cylinder die casting mold. In addition to the closed cycle system, they also use a computer control system, and the temperature of each point on the mold can be set by computer. The mold is equipped with a sensor to detect the temperature of each part, and the temperature is converted into an electrical signal and fed back to the computer control system to compare with the set temperature to adjust the flow of cooling water everywhere.
5. Closing remarks
The cooling water in the complex mold directly affects the life and quality of the mold. For a complex mold such as a die-casting cylinder, there are hundreds of cooling water inlet and outlet pipes, and the cooling water in each part of the mold should be adjusted accordingly. If the valve is used, not only the layout is difficult, but also the quantitative adjustment cannot be achieved. Only by using computer control system, can it be easy to adjust and stabilize the temperature of each point of the mold.
The structure of the mold, the wall thickness and complexity of the workpiece, the change of temperature, etc., have different requirements for the cooling water flow of the mold, which needs to be tested and explored for a certain time to obtain the best data.