Shenzhen quality die casting manufacturing injury experience sharing!!!
Release time:2024-05-15
Shenzhen quality die casting manufacturing injury experience sharing!!!
Recently, we encountered a very typical zinc alloy die casting customer case. A customer's sample was delivered in a very tight time, and the sample delivery time was compressed to only 9 days. After we worked overtime to open the mold for him, it was finally time to open the mold and produce the sample. Due to the problems of wall thickness and through holes on the product drawings, the mold was not smooth, deformation and surface treatment bubbles and other defects resulted in a lot of scrap! We must sum up our experience and draw lessons.
First let the zinc alloy die casting molding, the size of the shrinkage will occur, and the influence of the larger alloy composition on the size of the zinc alloy castings, the size of the copper is relatively stable, small size changes in general zinc aluminum alloy castings. When the working area of zinc alloy is narrow and the temperature is lower than 0℃, the impact toughness decreases sharply. When the temperature exceeds 100℃, the mechanical properties decrease significantly. The aging, re-expansion and strength reduction of zinc alloy will cause aging phenomenon and reduce the shaping performance.
The main reason is because the solubility of lead, tin, and impurities such as zinc and cadmium are too small. Therefore, the material and melting should strictly control the content of impurities. Secondly, we must master the chemical properties of zinc alloy die casting, zinc alloy die casting in the die casting process, the influence of technology will produce zinc and aluminum rich zinc alloy part. Aluminum rich phase is preferred to dissolve, zinc acid phase is preferred to dissolve. If in addition to strong alkali or acid oil or the use of etching process, electroplating can cause foaming, coating off, seriously affecting the product yield. Therefore, zinc alloy die casting should not be strong acid or alkali degreasing, pickling.
Finally, to the big aspect, the die casting industry is a major polluter of mechanical production, all engineering and technical personnel in the work practice, to be good at repeated research, summarize the past lessons and experience, to learn lessons to improve the traditional design concept, fully understand efforts to improve the process yield and blank utilization rate, is an effective way to save energy and reduce emissions in the field of die casting, is of great significance, Today, with the vigorous development of industry, reducing environmental pollution is everyone's responsibility, only we can carry such a big responsibility in every position.
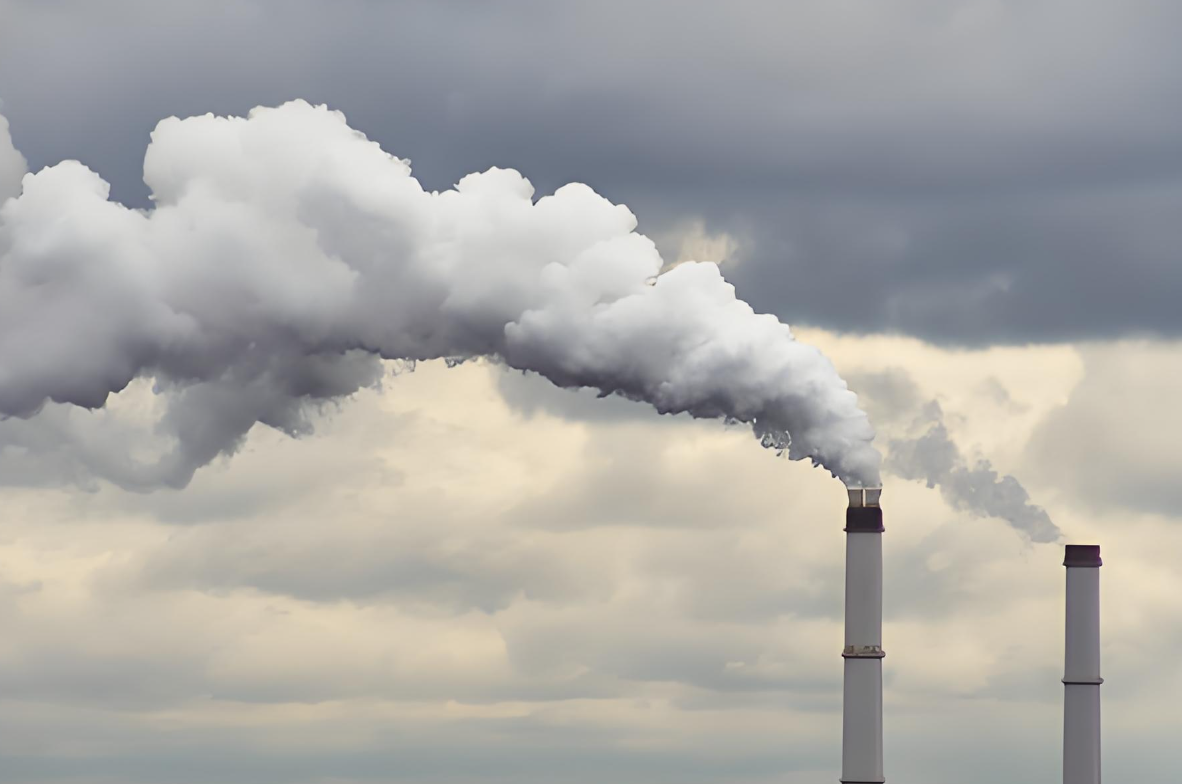