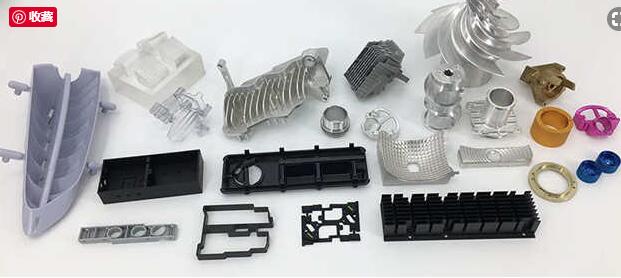
6 High-speed Machining Tips for Milling Aluminum
Compared with conventional milling, high-speed aluminum milling is a more innovative and productive way to manufacture low-volume parts & prototypes.
Categorys:CNC Aluminum Machining
Aluminum milling.-feature image
The modern industry needs parts done very fast. Rapid prototypes or custom parts demand to rise higher every month. The clients want their orders faster and need the components to have more accuracy than before. One of the most widespread alloys for modern production is aluminum, seemingly the best material there can be. It is lightweight, strong, durable, and resistant to corrosion. That's why new milling aluminum strategies are developed rapidly.
One of the modern successful CNC aluminum milling methods is called High-Speed Machining. The main difference compared to conventional milling is that the speeds of high-speed milling are considerably higher, and with them, the machinists can increase cutting feeds. As a result, HSM milling aluminum is very advantageous in a number of unexpected ways. Here is what you will gain by choosing HSM strategies for aluminum instead of using conventional milling.
The Efficiency is Much Higher
By increasing the cutting speed up to 3 times as fast as conventional aluminum milling, it is possible to increase the feeds up to 2 times ( in cases for softer aluminum alloys ). As far as we know, machining feeds are the parameters that define the productivity of the whole milling process. That being said, high-speed machining efficiency can be much compared to conventional milling. Aluminum machinability makes it possible to increase spindle revolution speeds up to 18000 rpm and more, thus making material removal rates scary.
Such material removal rates make aluminum machining services using HSM strategies for aluminum a very lucrative offer for automotive and aerospace industries. In the first case, automotive prototypes require a lot of material removal with preferably as few milling setups as possible. In the second case, there are a lot of long and large parts that have deep pockets ( they must be lightweight so they are mostly machined down to a set of intersecting ribs) and thin walls, in addition, aluminum alloys are what planes and rockets consist of up to 80%.
The Temperature of the Cut
It has been proved that the temperature of the cut changes with the increase of the speed. At first, as the speed grows, so does the temperature. However, as we go further, the temperature starts to go down drastically until, at some point, it stops to matter. Increasing cutting velocity will only lower the temperature to a small degree. This transition is what signifies HSM. For example, when milling aluminum at 300-500 m/min, the temperatures may reach 600-800 degrees. However, if we increase the velocity up to 1200, the temperature goes down to less than 200 degrees, and it is a mere 150 degrees at 1800 m/min. From that point on cutting faster is pointless.
Just consider, a mere 150-200 degrees! No material property change in the area of the cut due to local thermal processing, no metal grain increase, and much smaller demands to cooling. A good advantage, I'd say.
Tools Live Longer
It may seem strange because the speed of the cut is larger and so tool wear must be as well, but if we compare the amount of material that gets cut by the aluminum cutting tools at HSM with conventional milling rather than tool life in minutes, we'll see that the difference is evident and speaks in High-speed milling aluminum favor. What's the reason for a prolonged tool life? First, the cutting temperature is lower and that means tool material strength is higher. Then, chip width during high-speed milling is much lower ( the tool turns faster and manages to cut off a thinner chip even despite increased feeds).
In addition, when machining aluminum, one of the main issues is that it is so soft, it sticks to the cutting edges of the tool during processing. This lowers tool sharpness and increases cutting forces hence decreases tool life. But that doesn't happen at high speeds. Aluminum just leaves.
Ready to start your new project now?
The Precision of High-Speed Milling Aluminum
We all think that higher feeds make the aluminum surface finish lower because the tool cutting edge travels further while the tool can make a turn and cut it off. Generally, this results in a wider chip, higher cutting force, and a worse surface finish. However, in HSM despite the feed being larges, the velocity of the tool is higher, so the chip is actually thinner than in conventional milling. In addition, vibration is lower because of a smaller cutting force.
Constant Tool Engagement Angle
One of the major problems when milling part cavities with end mills is concerned with manufacturing pocket angles. The end mill must turn 90 degrees in order to produce the pocket and at that moment, the material it has to cut doubles ( from both sides of the pocket). This results in a local increase in cutting force and is very bad for tool life and part precision. However, HSM aluminum milling has a number of predetermined tool path generation strategies that include a constant tool engagement angle. That means the tool gets gradually closer to the angle while machining all the material around it in a circular trajectory. That way, the cutting force remains constant and so does the precision. in addition, tool life is prolonged.
Coolant Use
Some HSM strategies for aluminum machining don't use coolants at all. I mean, machining at 200 degrees hardly requires any cooling of both the material and the cutter. However, some extremely precise operations still use coolants in order to increase part quality but the quantity of the coolant is much lower compared to conventional machining. Some aluminum high-speed milling processes use the so-called minimum quantity lubrication. The amount of coolant administered is just enough to make a thin film that lowers friction and offers some cooling.
So, it is quite evident that High-speed aluminum milling is an innovative and productive way to manufacture custom parts, prototypes, small batches, and other sets made of aluminum alloys. With high-speed machining, you will get better prices and will spend less time waiting for your order to be fulfilled.
Aluminum as a material offers some interesting thermal and mechanical properties. Besides, the aluminum metal is relatively easy to shape, especially in drilling processes, like in CNC aluminum machining. In fact, we highly regard an aluminum alloy compared to other lightweight metals such as magnesium and titanium alloys.
The use of CNC aluminum has grown immensely, the production of CNC automotive parts and other CNC parts that are lightweight has been intense. Below are a few of the things you may not have known.
Aluminum Material: CNC Aluminum Machining
Aluminum is soft, lightweight, tractable, malleable, and durable metal. Its appearance is silver or dull grey and depends on the roughness of the surface. It lacks magnetic properties and its non-flammable. The aluminum metal melts at 640 degrees, and it’s light with a density of 2.68. It is a good conductor of electricity though not of the same standard as copper on specific cross-section area and is widely used in CNC automotive like ATV, Aerospace and medical industries.
Aluminum Grade
The ultimate choice of the type of aluminum grade you intend to use depends on your machining projects, which allow you to rank each grade according to its characteristic, from the most important to the least. By doing so, you get to choose the aluminum of specific properties and shape as per your needs.
The following are some types with essential facts about Aluminum grade;
Aluminum 6061: This grade has superb mechanical properties, excellent weldability. Its topical properties make it one of the most extruded grade. This is because of its good toughness, medium and high strength, excellent corrosion resistance on harsh condition, cool anodization, and bending workability. Aluminum 6061 is commonly used for 5 axis CNC machining.
Aluminum 7075: It’s also popular even though not like the 6061. This grade is known for its exceptional fatigue strength. This aluminum grade is not suitable for welding; it’s costly. Hence, it is better for tough parts, such as fuselages, bicycle parts, rock climbing kits, and aircraft wings. This alloy also better in corrosion resistance.
Aluminum 2024: The alloy is predominantly used in military and aerospace sector. This is because of its mechanical properties, like great weariness resistance, and high strength. The aluminum 2024 is terrible in corrosion resistance and not weldable.
CNC Aluminum Prototype
Aluminum machined prototype are commonly produced according to a variety of alloys. The most used alloy is the 6061-T6, this caters for electronics, transportation, aerospace, military industries among others.
Aluminum alloys are low in density but high in strength. Often CNC aluminum prototype machining has the vast tolerance to control even 0.01MM. The CNC machine can manufacture unique and quality aluminum prototypes. CNC milling is just the perfect choice, the advantages are in the machining process, and that is the high precision and milling aluminum.
CNC Machined Aluminum Components and Parts
The technology of CNC machined aluminum has produced CNC parts and components that aid in a wide range of services (Turning, milling and grinding). Today, well machined CNC aluminum parts are growing in popularity in the engineering sector.
The following are some of the CNC machined aluminum parts:
Front panels
Dowels Pins
EMI-Housings
Spline Shafts
Medical Devices
Lighting Fixtures
How to avoid deformation in CNC aluminum machining
Aluminum is an essential industrial material, but it has a major undoing. The alloys contain relatively low hardness and their thermal expansion are high, can deform when being machined into a thin part. However, several steps can be taken to avoid the deformation of the material beforehand.
Symmetrical Machining
It’s essential to avoid extreme concentration of heat but rather to create a dissipation of heat to reduce the rate of thermal deformation.
Stratified Multiple Machining
If you have several cavities on some aluminum alloy plate, you can easily twist one cavity wall because of the force distribution. To avoid such an occurrence, you should process all cavities in the same period.
Get an Appropriate Cutting Parameter
The significant influence on the cutting parameter is the amount of cutting back depth. To maintain efficiency and reduce the number of cutting. A CNC milling can settle the problem, by increasing the speed of the machine and reducing the cutting force.
Drilling and Milling
When the milling cutter is applied to cavity and parts, the cutting is sufficient. The leads to cutting heat, expansion, and deformation. The best way of avoiding this problem is pre-drilling with a bigger tool than the milling cutter and then put the milling cutter and mill.
5 Axis CNC Machining
On the 5-axis machining, the CNC moves while cutting in five angles of the axes simultaneously. This machining process is fast, reliable on designing complex parts, as work is approached in multiple directions.
The 5-axis machining has been adopted widely because of the following:
The set-up is a single one, and this reduces the lead time and better the efficiency
It allows better geometry due to its ability to avoid collision with the tool holder tilting the table or the cutting tool.
Can use shorter tools that are more rigid, some with high spindle speeds rate which is achieved by reducing the load cutting tool.
Pieces don’t pass through different workstation hence errors are reduced, accuracy maintained, and quality is guaranteed.
As we conclude, you are now aware of the various CNC machined aluminum process (milling, drilling, and turning) that unfinished piece of aluminum is taken through until it becomes a complete product. It’s an arduous process that requires experience, accuracy, and powerful machinery. Moreover, these are because of the different aluminum alloy used.
The benefits of aluminum are obvious: fantastic cutting process, the best quality and the demand for a machined aluminum product is on the rise. Industries are snowballing with many specialists to meet your needs, remember to do your research and seek samples to be sure on the quality of the CNC aluminum.